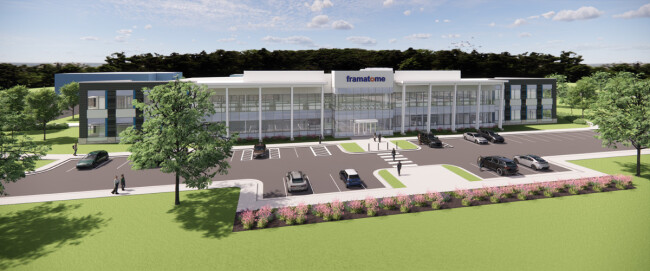
All news
about Framatome’s nuclear activities
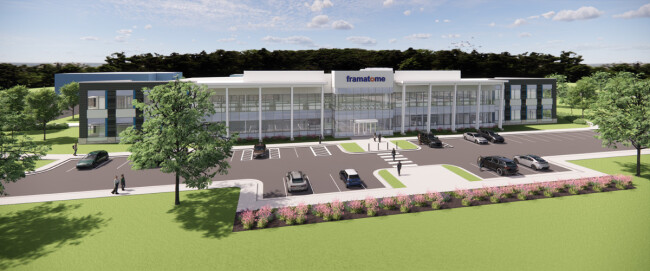
Press Release
Framatome breaks ground on $50 million expansion in Lynchburg, Va.
April 25, 2024 - Representatives from Framatome were joined today by local dignitaries to break ground on the $50 million expansion of its Mill Ridge...
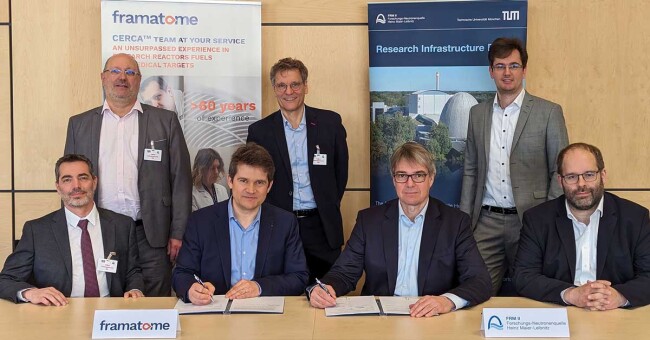
Press Release
Framatome to start industrialization of Europe’s first high-density monolithic nuclear fuel for research reactors
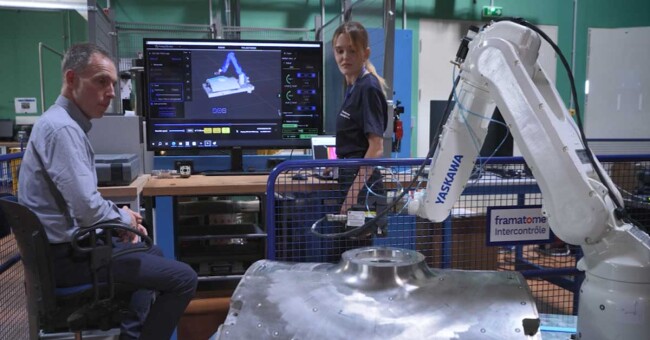
Article
Non-destructive testing: cutting-edge technologies for in-service reactors
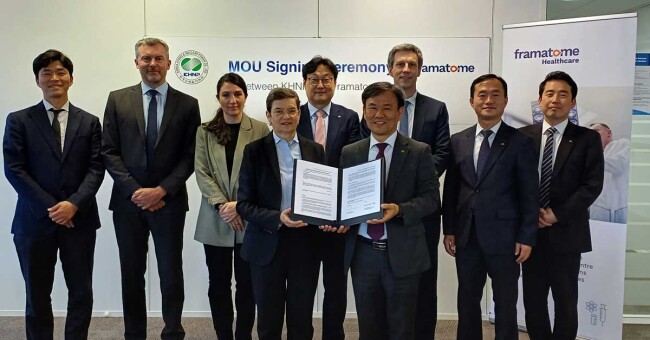
Press Release
Framatome and KHNP to assess feasibility of medical isotope production at South Korean nuclear power...
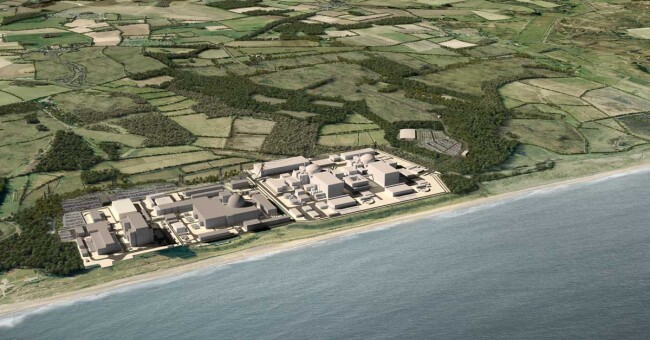
Press Release
Framatome has signed contracts worth multi-billion euros for Sizewell C in the UK
Blockchain
Blockchain-certified press releases
All our press releases are certified by the blockchain. In this space, check that our press releases are certified and not modified by a third party.
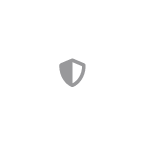
Import or drag our press releases in pdf format into this insert.