
All news
about Framatome’s nuclear activities

Press Release
Framatome receives U.S. Safety Authority approval to transport higher enriched fuel to light water reactor...
Framatome is pleased to announce that the U.S. Nuclear Regulatory Commission (NRC) approved a license amendment allowing transport of fresh nuclear fuel assemblies in the...

Press Release
The Steam Generator Replacement Team joint venture signs $700 million contract for steam generator replacements...

Press Release
Framatome to engineer and install reactor vessel closure head replacement for Arkansas Nuclear One

Press Release
Framatome to supply fuel to VVER reactors in Slovakia

Press Release
Framatome Inc. welcomes Tony Robinson as new Chief Executive Officer
Blockchain
Blockchain-certified press releases
All our press releases are certified by the blockchain. In this space, check that our press releases are certified and not modified by a third party.
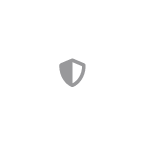
Import or drag our press releases in pdf format into this insert.