Nuclear power: a source of controlled, low-carbon, affordable energy
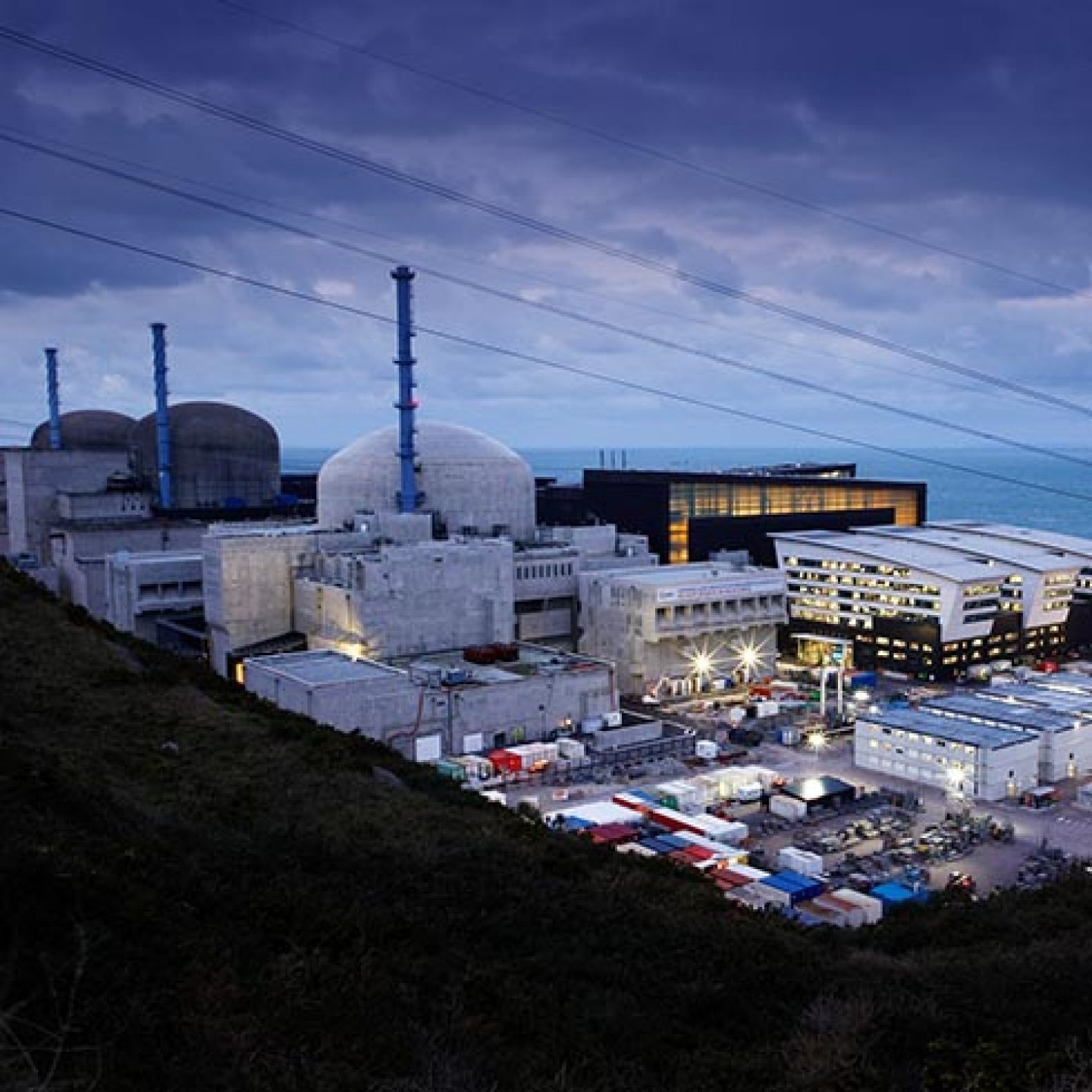
View of Flamanville 3, 2 and 1 - © EDF
View of Flamanville 3, 2 and 1 - © EDF
Faced with global warming and sharply increasing demand for electricity, nuclear power is an essential solution.
We have been designing and manufacturing high-performance components, fuels, and instrumentation & control (I&C) systems for all types of nuclear reactors for more than 60 years. We provide maintenance and offer a comprehensive range of services so that you can be sure to get the most out of your generating facilities.
We offer proven solutions for a cleaner, safer and economical low-carbon energy mix.