Innovating to maintain the competitiveness of nuclear energy

Framatome is innovating in many fields to improve the competitiveness of its customers and nuclear energy.
Our teams work to develop new solutions for maintaining facilities in operating condition and extending their lifespan, thus improving the durability of our industry. For example, the robotics solutions and new imaging technologies we have developed make it possible to reduce the duration, and therefore the cost, of outages.
In coordination with the industry, Framatome has also initiated a digital transformation to boost its operational efficiency: paperless documents, leveraging xR technologies (virtual, augmented and mixed reality) across all of our businesses, capitalizing on our data, etc. Already in place at Framatome, these new solutions will fundamentally transform our industry to ensure that nuclear becomes an energy of the future.
Several examples:
Additive manufacturing: specific processes for demanding applications
Through additive manufacturing, Framatome deploys advanced manufacturing techniques to meet the nuclear industry requirements with efficient and economical solutions. The diversity of processes makes it possible to offer tailor-made, innovative and optimized solutions for applications as varied as the components manufacture or rapid maintenance.
Framatome uses the techniques of melting points on a powder bed, deposition under concentrated energy, projection of material and projection of binder to manufacture metal parts with complex geometries that would be impossible to obtain with traditional processes. The outlets for these processes in the nuclear industry cover various fields of application:
- Maintenance, through the manufacture of spare parts, specific implements and extensive repair possibilities
- Manufacturing of small components
- The addition of functions on massive components of the ‘nuclear island’
Framatome is committed to the entire value chain in a global approach and qualification process:
- Design for additive manufacturing
- Control of processes and removal of technological barriers related to manufacturing quality
- Knowledge and mastery of material properties
- Study of behavior in service
- Control measures
In this initiative, Framatome has surrounded itself with a solid ecosystem of industrial and academic partners and benefits from the support of the Research & Development programs of the European Union and the United States Department of Energy (DOE).
Important facts:
- Over 30 application cases already developed
- Irradiation of the first components produced by additive manufacturing
- Involvement in standardization and qualification committees
- Integration of topological optimization and design rules during the design process
- Establishment of material files
A new generation of Reactor Control based on Artificial Intelligence named COCOAI
A nuclear reactor is a complex system and its comprehensive control is not trivial. As flexible operation becomes an increasingly bigger stake for nuclear, classical control technology reaches its applicability limits. Fortunately, artificial intelligence comes to the rescue and allow a smart and safe augmented control of the reactor, taking care of its multiple aspects. Framatome leverages this technological brick for more flexibility in operating nuclear reactors: focus on COCOAI, one of its application.
Framatome proposes a new approach for governing of PWR based on Artificial Narrow Intelligence (ANI). Contrary to control technology, ANI allows consideration of an arbitrary large number of goals even if quite different in nature. In this case, safety, ergonomics, operation economy and grid services can be processed simultaneously in accord with each other. The scope of goals can be easily extended every time.
Thus, Core Control Based on Artificial Intelligence (COCOAI) can generate not only control commands in real time, it can also compile comprehensive plans for control actions for the next 24 hours, continuously update these plans and permanently display them to the operator along with predicted trajectories for all important process variables for this time horizon.
COCOAI proposes three possible operation modes:
- Manual: the Reactor Core Governor serves as an operator assistance system (OAS) showing the predicted trajectories of all important process variables for the next 24 hours, together with the automatically compiled plan for control actions for this time span and proposing these control actions in real time. If the operator executes the proposed control action, process variables remain in the current plan; if the operator ignores the proposition or makes some unproposed actions, COCOAI will, like a street navigator, quickly compile a new plan and display it.
- Semi-automatic: the operator pushes and holds the ‘enable’ button and the Core Governor automatically performs the control actions while the ’enable’ button is pushed.
- Automatic: pushing of the ‘enable’ button is not more necessary. The operator observes the process and its prediction on a screen having the possibility each time to deselect the fully automatic mode and to perform further control of boration/dilution system (Bo/Di) and possibly heavy bank of control rods (H-bank) manually.
Primary advantages
- Enhance flexibility of the NPP
- Enable highly economical operation
- Can be applied to all existing PWR as an update
- Prediction provider
Reconstructing images from video to improve safety at nuclear plants
Designed and patented by our teams, the “stitching” method makes it possible to reconstruct images from video during visual inspections of nuclear components.
Technicians can now analyze data with greater ease, reliability and speed. They can also move and zoom images just as they would with an interactive map. That way they can focus on indicated or suspect areas of components on the micrometer level and extract images to compile their final report.
The image reconstruction software represents a disruptive advance over previous analysis methods. Previously, in order to detect anomalies, operators would need to focus on each moment in a video stream or analyze the data on their computer screens.
Primary advantages
- More reliable analyses
- Faster analyses
- Inspection of the entire area
- High image quality/Compatible with numerous video formats
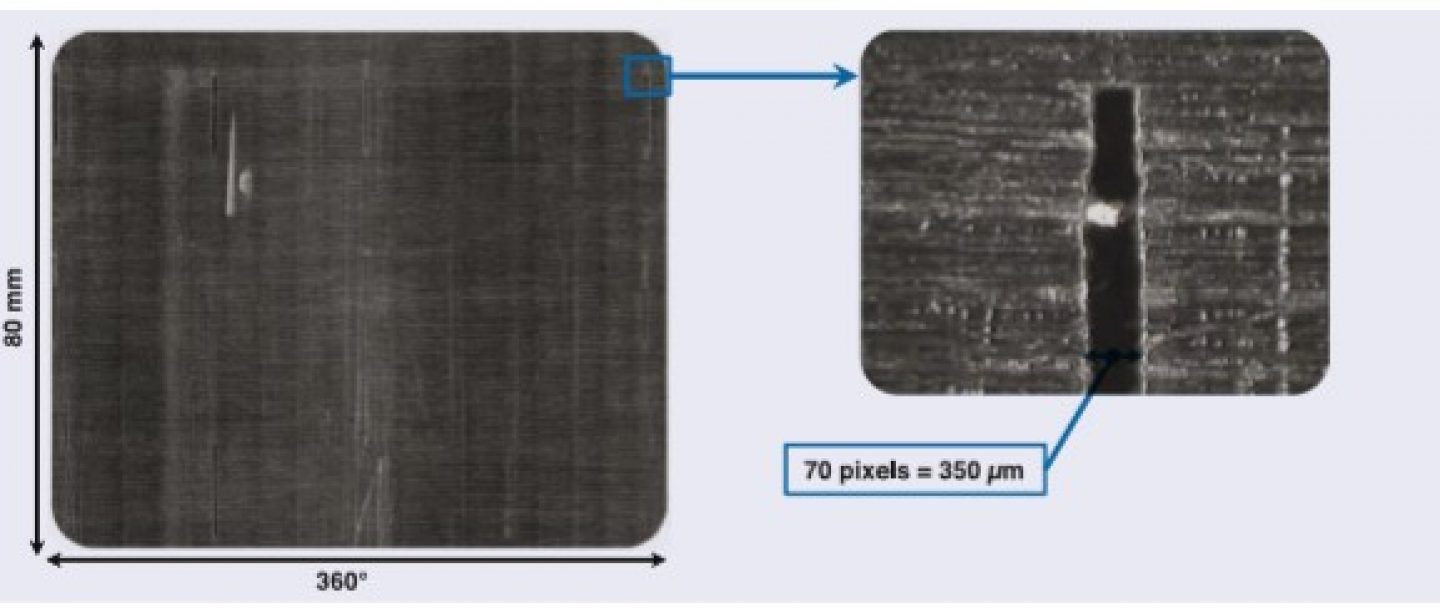