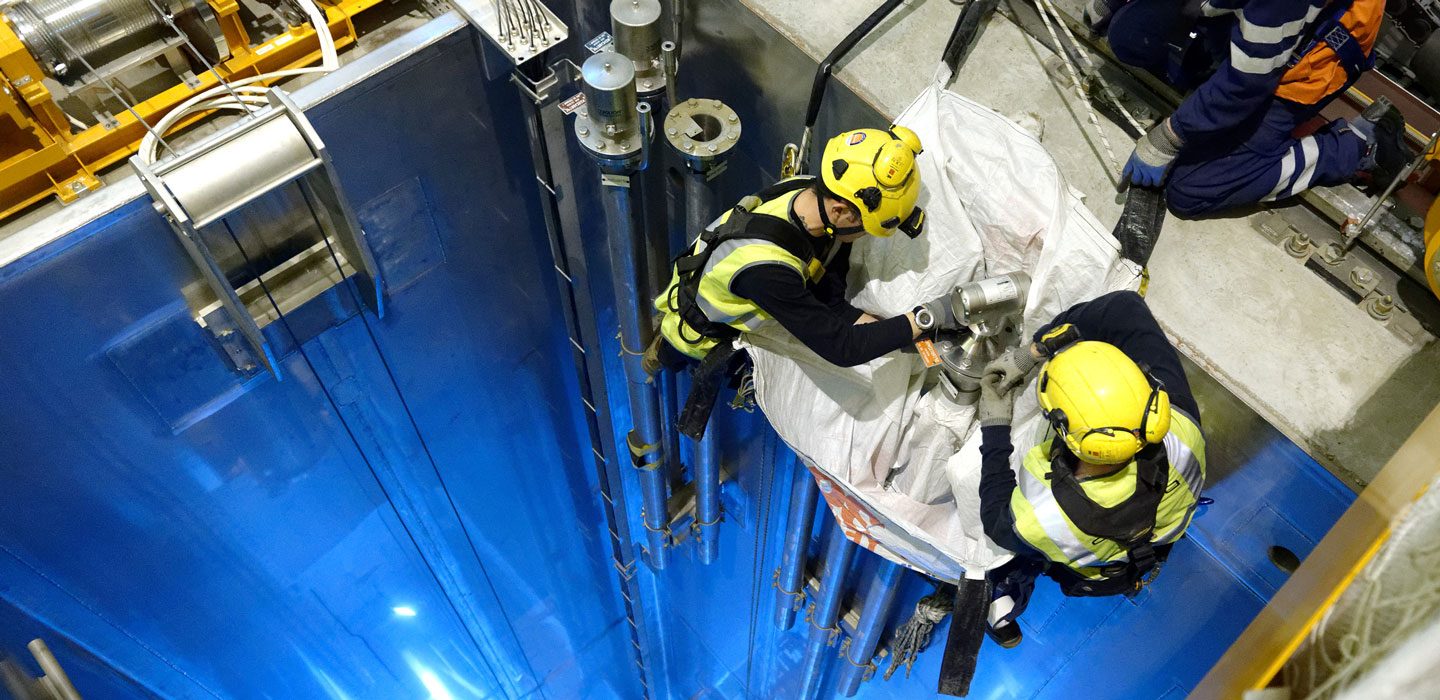
International leader in nuclear energy
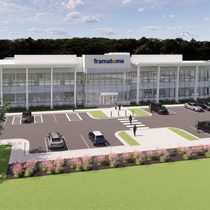
Framatome breaks ground on $50 million expansion in Lynchburg, Va.
Find out more
Framatome’s teams design, build and service the nuclear steam supply system (NSSS). For more than 60 years, the company has been present at every stage of the process on all types of reactor technologies.
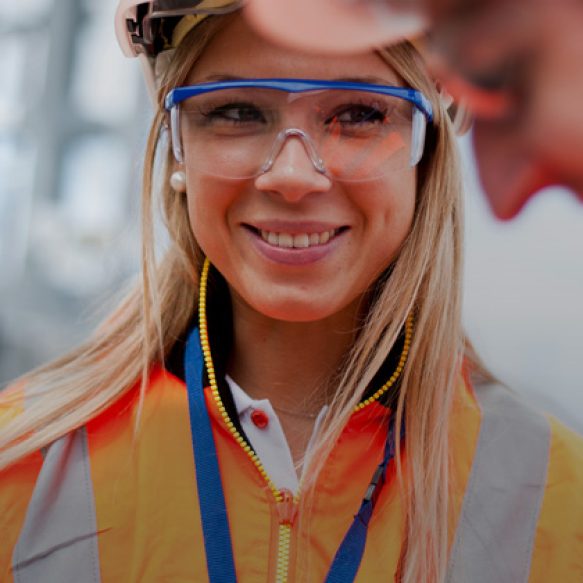
We are recruiting
Like you, we want a brighter future.
Together we will enable clean, safe and economical low-carbon energy to meet the global ambition for a better tomorrow.
Together we will enable clean, safe and economical low-carbon energy to meet the global ambition for a better tomorrow.
Discover Framatome
Framatome is a NSSS designer and manufacturer, supplier of equipment, services and fuel for high levels of safety and performance
€4 billion
in revenue in 2023
18,000
employees of all nationalities
64
sites worldwide
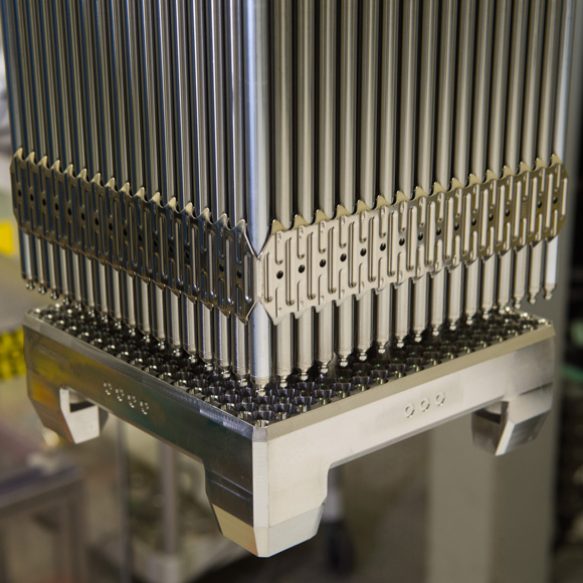
Featured solution
PROtect program: Enhanced Accident Tolerant Fuel assemblies (E-ATF)
PROtect provides improved fuel reliability due to increasing wear resistance, very low oxidation kinetics under high-temperature steam and increased fission gas retention
PROtect provides improved fuel reliability due to increasing wear resistance, very low oxidation kinetics under high-temperature steam and increased fission gas retention